Usage:
Access Free Cat Ecm Manual Guide View ID 2201680d2 Apr 11, 2020 By Astrid Lindgren 2020 read cat ecm manual guide by erle stanley gardner cat workshop pdf manuals are in demand in all countries in the world and we have provided cat pdf files to more than 50 countries the price is the Cat Ecm Manual Guide - hibeato.bourseaccrochecoeur.ca. CATERPILLAR Diesel engine C15, C-15, C-16, C16, C-16, C18, C175-16 Parts Catalogs, Service (workshop) Manuals, Operation and Maintenance Manuals in PDF format. Spare parts for Caterpillar diesel engines. Caterpillar C32 Manuals & User Guides User Manuals, Guides and Specifications for your Caterpillar C32 Engine, Portable Generator. Database contains 1 Caterpillar C32 Manuals (available for free online viewing or downloading in PDF): Operation and maintenance manual. Caterpillar C32 Operation and maintenance manual (144 pages). 12 pl1000t communication ecm.114. 12.1 configuring the pl1000t communication ecm.
826K2L3Removal Procedure
Required Tools | |||
---|---|---|---|
Tool | Part Number | Part Description | Qty |
A | 5F-4764 | Pry Bar | 1 |
B | 8T-2998 | Lubricant | 1 |
C | 1U-5718 | Vacuum Pump | 1 |
169-7372 | Fluid Sampling Bottle | 1 | |
4C-4057 | Tube 7.9 mm(0.31 inch) OD | 1 | |
D | 4C-5552 | Large Bore Brush | 1 |
E | 4C-6774 | Vacuum Gun Kit | 1 |
F | 8T-7765 | Surface Reconditioning Pad | 1 |
Start By:
- Remove the rocker arms and the rocker arm shaft.

NOTICE |
---|
Keep all parts clean from contaminants. Contaminants may cause rapid wear and shortened component life. |
- Disconnect harness assembly (1).
- Remove bridge assemblies (3). Show/hide table
NOTICE If the injector hold down bolt is loose during the removal procedure, inspect the injector bore for wear and debris. Replace the clamp and spacer.
- Remove bolt (4) and spacer (5).
- Place an identification mark on electronic unit injectors (2) for installation purposes. Each electronic unit injector must be reinstalled in the original location in the cylinder head.
- Use Tooling (A) to pry beneath the base of clamp (6) and free electronic unit injector (2).
- Remove clamp (6) and electronic unit injector (2) from the cylinder head.
Illustration 1 | g02343936 |
Installation Procedure
NOTICE |
---|
Keep all parts clean from contaminants. Contaminants may cause rapid wear and shortened component life. |
- Use Tooling (C) to remove the fuel and oil from the cylinder. Evacuate as much fuel and oil as possible from the cylinder before installing the electronic unit injector. Several evacuations may be necessary.
- Use Tooling (D) to clean the carbon deposit from the inside of the electronic unit injector sleeve. Tooling (E) is available to clean loose material from the bore of the electronic unit injector sleeve and the cylinder.
- Use Tooling (F) to clean the carbon from the seat area that is inside of the electronic unit injector sleeve.
- Install the O-ring seals on the electronic unit injector. Lubricate the top two O-ring seals with a 50/50 mixture of clean engine oil and Tooling (B). Show/hide table
Illustration 2 g02343936 Illustration 3 g01135876 - The E-Trim value must be programmed into the engine control module when you install a new injector . Program the injector confirmation code into the engine control module. E-Trim Value (X) is a 12 digit alphanumeric code that is supplied with the data sheet that comes with the new injectors. Injector Confirmation Code (Y) is a four digit numeric code. Both of the codes are located on the top of electronic unit injector (2). Use the following menu to program the E-Trim value.
- ECM Summary Screen
- Service Menu
- Calibration
- Injector Code Calibration
Show/hide tableNOTICE When an electronic unit injector is replaced, the new electronic injector code must be programmed into the engine's personality module software by using the calibration menu on the Electronic Service Tool. If the new electronic injector code is not entered, the characteristics of the previous electronic unit injector is assumed.
If it is not possible to immediately reprogram the electronic injector code into the personality module software, the engine will not be severely harmed. The new electronic injector code should be reprogrammed as quickly as possible in order to optimize engine performance.
- Position electronic unit injector (2) and clamp (6) in the cylinder head.
- Install spacer (5) and bolt (4). Tighten the bolt to a torque of 55 ± 10 N·m(41 ± 7 lb ft).
- Install bridge assemblies (3).
- Connect harness assembly (1).
End By:
- Install the rocker arms and the rocker arm shaft.
Cat C32 Ecm Manual Pdf
Usage:
C27AT4System Operation Description:
Use this procedure to troubleshoot the electrical system if a problem is suspected with either of the engine speed/timing sensors. Also, use this procedure to troubleshoot the electrical system if any of the diagnostic codes in Table 1 are active or easily repeated.
Diagnostic Trouble Codes | ||
---|---|---|
J1939 Code and Description | Conditions that Generate the Code | System Response |
190-8 Engine Speed : Abnormal Frequency, Pulse Width, or Period | The signal from the primary engine speed/timing sensor is intermittent or the signal has been lost. | The engine will use the signal from the secondary engine speed/timing sensor for engine speed/timing. The code is logged. |
637-13 Engine Timing Sensor : Out of Calibration | the engine has failed the automatic timing calibration during engine start-up | The value of the timing offset that has been stored in memory will be used. This value will continue to be used for the timing calibration until the diagnostic is resolved The code is logged. |
723-8 Engine Speed Sensor #2 : Abnormal Frequency, Pulse Width, or Period | The signal from the secondary engine speed/timing sensor is intermittent or the signal has been lost. | The engine will use the signal from the primary engine speed/timing sensor for engine speed/timing. The code is logged. |
The engine uses two engine speed/timing sensors. The primary speed/timing sensor detects the reference for engine speed and timing from a timing ring on the crankshaft timing gear. The timing ring consists of a notched pattern that is machined onto a portion of the gear. The signal from the primary engine speed/timing sensor is also used by the Electronic Control Module (ECM) as a control reference during a timing calibration.
The secondary engine speed/timing sensor detects the reference for engine speed and timing from a timing ring on the camshaft timing gear. The timing ring consists of a notched pattern that has been machined onto a portion of the gear.
The ECM counts the time between pulses that is created by the sensor as each gear rotates in order to determine rpm. Timing is provided by the unique pattern of notches in the timing ring.
Under normal operation, the secondary engine speed/timing sensor is used to determine timing for starting purposes. The secondary engine speed/timing sensor is used to determine when the piston in the No. 1 cylinder is at the top of the compression stroke. When the timing has been established, the primary engine speed/timing sensor is then used to determine engine speed.
When the timing has been established, the ECM triggers each injector in the correct firing order at the correct time. The actual timing and duration of each injection is based on engine rpm and on load.
If the engine is running and the signal from one sensor is lost, no change in engine performance will be noticed. If the engine is running and the signals from both sensors are lost, fuel injection will be terminated. The engine is shut down by the ECM.
The engine will start when only one sensor signal is present. The engine will not start if the signals from both sensors are lost.
A timing offset is determined during each engine start-up. The value of the timing offset is stored in the non-volatile memory of the ECM until the successful completion of the next engine start-up. If a failure mode for the crankshaft speed/timing sensor is detected during engine start-up, the timing offset stored in ECM memory will be used. This value will continue to be used for the engine timing calibration until the diagnostic is resolved. A timing calibration cannot be performed manually on this engine.
Both sensors are magnetic sensors. The two sensors are not interchangeable. If a sensor is replaced, a timing calibration is not necessary.
Complete all of the following tasks when you install a speed/timing sensor:
- Ensure that an O-ring is installed on the sensor. If the O-ring is damaged or missing, replace the O-ring.
- Lubricate the O-ring with oil.
- Ensure that the sensor is fully seated into the engine before tightening the bracket bolt.
- Ensure that the electrical connector is latched.
- Ensure that the harness is properly secured, and ensure that each tie-wrap is placed in the correct location.
Illustration 1 | g02128717 |
Schematic for the engine speed/timing sensors |
Test Step 1. Check for Diagnostic Codes
- Connect Cat ET to the service tool connector. Refer to Troubleshooting, 'Electronic Service Tools'.
- Restore electrical power to the ECM.
- Start the engine and run the engine until the engine is at the normal operating temperature.
Note: If the engine will not start, monitor the engine rpm on Cat ET while the engine is being cranked. You may need to power Cat ET from another battery while the engine is being cranked.
- Look for these codes on Cat ET:
- 190-8
- 723-8
Expected Result:
One or both of the diagnostic codes that are listed above are logged or active.
Note: If the engine will not start and Cat ET displayed 0 rpm during cranking, select 'No Engine rpm'.
Results:
- No Engine rpm - Engine rpm is not indicated on Cat ET. Proceed to Test Step 2.
- Active 190-8 or 723-8 Code - There is an active diagnostic code or a logged diagnostic code for an engine speed/timing sensor. Proceed to Test Step 4.
- Active 637-13 Code - The ECM was unable to calibrate the engine timing during the previous start-up attempt. Proceed to Test Step 2.
- No codes - Neither code is active or logged.
Repair: Refer to the appropriate symptoms in Troubleshooting, 'Troubleshooting Without a Diagnostic Code'.
STOP
Test Step 2. Check the Installation of the Sensor Assembly
- Remove electrical power from the ECM.
Illustration 2 g01167684 Typical engine speed/timing sensor
(1) Mounting flange
(2) Mounting surface - Visually inspect each sensor assembly without removing the sensor assembly from the engine. Ensure that flange (1) is installed squarely against surface (2).
- Remove the suspect sensor assembly from the engine. Show/hide table
Illustration 3 g01167704 Typical engine speed/timing sensor
(3) O-ring - Ensure that one O-ring (3) is installed on the sensor. Check the O-ring for damage. Replace the O-ring, if necessary.
Results:
- OK - The sensor components are OK.
Repair: Perform the following procedure in order to install the sensor assembly:
- Lubricate the O-ring with engine oil.
- Fully seat the sensor assembly in the engine.
Note: If the sensor assembly will not fully seat into the engine, replace the sensor assembly.
- Tighten the bracket bolt.
- Connect the sensor electrical connectors. Verify that the connectors are latched on both sides.
- Ensure that the harness is properly secured, and that the tie-wraps are placed in the correct location.
Proceed to Test Step 3.
- Not OK - A problem has been identified with the speed/timing sensor.
Repair: Obtain a new sensor assembly. Perform the following procedure to install the sensor assembly:
- Lubricate each O-ring with engine oil.
- Fully seat the sensor assembly in the engine.
Note: If the sensor assembly will not fully seat into the engine, replace the sensor assembly.
- Tighten the bracket bolt.
- Connect the sensor electrical connectors. Verify that the connector is latched.
- Ensure that the harness is properly secured, and that the tie-wraps are placed in the correct location.
STOP
Test Step 3. Inspect the Electrical Connectors and the Wiring
- Thoroughly inspect connectors (4), (5), and (6). Refer to Troubleshooting, 'Electrical Connectors - Inspect'.
Illustration 6 g02129242 P2 terminals that are associated with the engine speed/timing sensors
(P2-25) Primary engine speed/timing −
(P2-35) Primary engine speed/timing +
(P2-46) Secondary engine speed/timing +
(P2-47) Secondary engine speed/timing − - Perform a 45 N(10 lb) pull test on each of the wires that are associated with the engine speed/timing sensors.
- Check the allen head screw on each ECM connector for the proper torque. Refer to Troubleshooting, 'Electrical Connectors - Inspect' for the correct torque values.
- Check the harness and the wiring for abrasion and for pinch points from each sensor back to the ECM.
Illustration 4 | g01167708 |
Location of the engine speed/timing sensors (typical front engine view) (4) Harness connectors for the secondary engine speed/timing sensor (5) Harness connectors for the primary engine speed/timing sensor |
Illustration 5 | g02133273 |
(6) J2/P2 ECM connector |
Expected Result:
All of the connectors, pins, and sockets are coupled and/or inserted. The harness and wiring are free of corrosion, of abrasion, and of pinch points.
Caterpillar C32 Cost

Results:
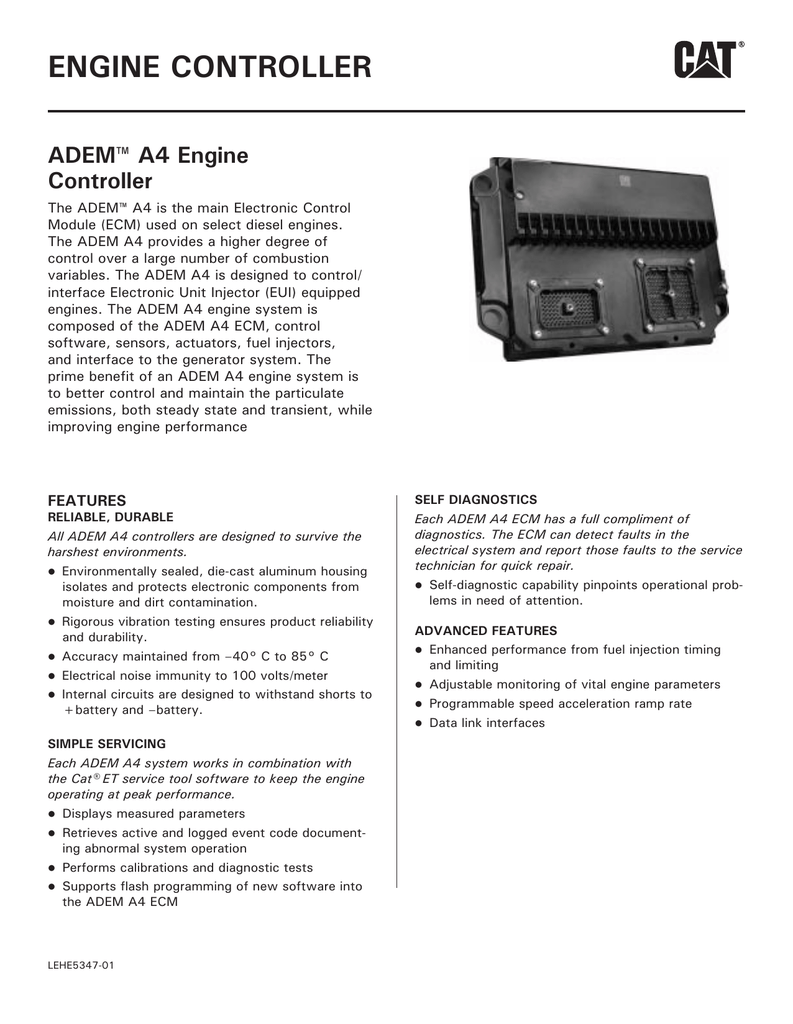
NOTICE |
---|
Keep all parts clean from contaminants. Contaminants may cause rapid wear and shortened component life. |
- Disconnect harness assembly (1).
- Remove bridge assemblies (3). Show/hide table
NOTICE If the injector hold down bolt is loose during the removal procedure, inspect the injector bore for wear and debris. Replace the clamp and spacer.
- Remove bolt (4) and spacer (5).
- Place an identification mark on electronic unit injectors (2) for installation purposes. Each electronic unit injector must be reinstalled in the original location in the cylinder head.
- Use Tooling (A) to pry beneath the base of clamp (6) and free electronic unit injector (2).
- Remove clamp (6) and electronic unit injector (2) from the cylinder head.
Illustration 1 | g02343936 |
Installation Procedure
NOTICE |
---|
Keep all parts clean from contaminants. Contaminants may cause rapid wear and shortened component life. |
- Use Tooling (C) to remove the fuel and oil from the cylinder. Evacuate as much fuel and oil as possible from the cylinder before installing the electronic unit injector. Several evacuations may be necessary.
- Use Tooling (D) to clean the carbon deposit from the inside of the electronic unit injector sleeve. Tooling (E) is available to clean loose material from the bore of the electronic unit injector sleeve and the cylinder.
- Use Tooling (F) to clean the carbon from the seat area that is inside of the electronic unit injector sleeve.
- Install the O-ring seals on the electronic unit injector. Lubricate the top two O-ring seals with a 50/50 mixture of clean engine oil and Tooling (B). Show/hide table
Illustration 2 g02343936 Illustration 3 g01135876 - The E-Trim value must be programmed into the engine control module when you install a new injector . Program the injector confirmation code into the engine control module. E-Trim Value (X) is a 12 digit alphanumeric code that is supplied with the data sheet that comes with the new injectors. Injector Confirmation Code (Y) is a four digit numeric code. Both of the codes are located on the top of electronic unit injector (2). Use the following menu to program the E-Trim value.
- ECM Summary Screen
- Service Menu
- Calibration
- Injector Code Calibration
Show/hide tableNOTICE When an electronic unit injector is replaced, the new electronic injector code must be programmed into the engine's personality module software by using the calibration menu on the Electronic Service Tool. If the new electronic injector code is not entered, the characteristics of the previous electronic unit injector is assumed.
If it is not possible to immediately reprogram the electronic injector code into the personality module software, the engine will not be severely harmed. The new electronic injector code should be reprogrammed as quickly as possible in order to optimize engine performance.
- Position electronic unit injector (2) and clamp (6) in the cylinder head.
- Install spacer (5) and bolt (4). Tighten the bolt to a torque of 55 ± 10 N·m(41 ± 7 lb ft).
- Install bridge assemblies (3).
- Connect harness assembly (1).
End By:
- Install the rocker arms and the rocker arm shaft.
Cat C32 Ecm Manual Pdf
Usage:
C27AT4System Operation Description:
Use this procedure to troubleshoot the electrical system if a problem is suspected with either of the engine speed/timing sensors. Also, use this procedure to troubleshoot the electrical system if any of the diagnostic codes in Table 1 are active or easily repeated.
Diagnostic Trouble Codes | ||
---|---|---|
J1939 Code and Description | Conditions that Generate the Code | System Response |
190-8 Engine Speed : Abnormal Frequency, Pulse Width, or Period | The signal from the primary engine speed/timing sensor is intermittent or the signal has been lost. | The engine will use the signal from the secondary engine speed/timing sensor for engine speed/timing. The code is logged. |
637-13 Engine Timing Sensor : Out of Calibration | the engine has failed the automatic timing calibration during engine start-up | The value of the timing offset that has been stored in memory will be used. This value will continue to be used for the timing calibration until the diagnostic is resolved The code is logged. |
723-8 Engine Speed Sensor #2 : Abnormal Frequency, Pulse Width, or Period | The signal from the secondary engine speed/timing sensor is intermittent or the signal has been lost. | The engine will use the signal from the primary engine speed/timing sensor for engine speed/timing. The code is logged. |
The engine uses two engine speed/timing sensors. The primary speed/timing sensor detects the reference for engine speed and timing from a timing ring on the crankshaft timing gear. The timing ring consists of a notched pattern that is machined onto a portion of the gear. The signal from the primary engine speed/timing sensor is also used by the Electronic Control Module (ECM) as a control reference during a timing calibration.
The secondary engine speed/timing sensor detects the reference for engine speed and timing from a timing ring on the camshaft timing gear. The timing ring consists of a notched pattern that has been machined onto a portion of the gear.
The ECM counts the time between pulses that is created by the sensor as each gear rotates in order to determine rpm. Timing is provided by the unique pattern of notches in the timing ring.
Under normal operation, the secondary engine speed/timing sensor is used to determine timing for starting purposes. The secondary engine speed/timing sensor is used to determine when the piston in the No. 1 cylinder is at the top of the compression stroke. When the timing has been established, the primary engine speed/timing sensor is then used to determine engine speed.
When the timing has been established, the ECM triggers each injector in the correct firing order at the correct time. The actual timing and duration of each injection is based on engine rpm and on load.
If the engine is running and the signal from one sensor is lost, no change in engine performance will be noticed. If the engine is running and the signals from both sensors are lost, fuel injection will be terminated. The engine is shut down by the ECM.
The engine will start when only one sensor signal is present. The engine will not start if the signals from both sensors are lost.
A timing offset is determined during each engine start-up. The value of the timing offset is stored in the non-volatile memory of the ECM until the successful completion of the next engine start-up. If a failure mode for the crankshaft speed/timing sensor is detected during engine start-up, the timing offset stored in ECM memory will be used. This value will continue to be used for the engine timing calibration until the diagnostic is resolved. A timing calibration cannot be performed manually on this engine.
Both sensors are magnetic sensors. The two sensors are not interchangeable. If a sensor is replaced, a timing calibration is not necessary.
Complete all of the following tasks when you install a speed/timing sensor:
- Ensure that an O-ring is installed on the sensor. If the O-ring is damaged or missing, replace the O-ring.
- Lubricate the O-ring with oil.
- Ensure that the sensor is fully seated into the engine before tightening the bracket bolt.
- Ensure that the electrical connector is latched.
- Ensure that the harness is properly secured, and ensure that each tie-wrap is placed in the correct location.
Illustration 1 | g02128717 |
Schematic for the engine speed/timing sensors |
Test Step 1. Check for Diagnostic Codes
- Connect Cat ET to the service tool connector. Refer to Troubleshooting, 'Electronic Service Tools'.
- Restore electrical power to the ECM.
- Start the engine and run the engine until the engine is at the normal operating temperature.
Note: If the engine will not start, monitor the engine rpm on Cat ET while the engine is being cranked. You may need to power Cat ET from another battery while the engine is being cranked.
- Look for these codes on Cat ET:
- 190-8
- 723-8
Expected Result:
One or both of the diagnostic codes that are listed above are logged or active.
Note: If the engine will not start and Cat ET displayed 0 rpm during cranking, select 'No Engine rpm'.
Results:
- No Engine rpm - Engine rpm is not indicated on Cat ET. Proceed to Test Step 2.
- Active 190-8 or 723-8 Code - There is an active diagnostic code or a logged diagnostic code for an engine speed/timing sensor. Proceed to Test Step 4.
- Active 637-13 Code - The ECM was unable to calibrate the engine timing during the previous start-up attempt. Proceed to Test Step 2.
- No codes - Neither code is active or logged.
Repair: Refer to the appropriate symptoms in Troubleshooting, 'Troubleshooting Without a Diagnostic Code'.
STOP
Test Step 2. Check the Installation of the Sensor Assembly
- Remove electrical power from the ECM.
Illustration 2 g01167684 Typical engine speed/timing sensor
(1) Mounting flange
(2) Mounting surface - Visually inspect each sensor assembly without removing the sensor assembly from the engine. Ensure that flange (1) is installed squarely against surface (2).
- Remove the suspect sensor assembly from the engine. Show/hide table
Illustration 3 g01167704 Typical engine speed/timing sensor
(3) O-ring - Ensure that one O-ring (3) is installed on the sensor. Check the O-ring for damage. Replace the O-ring, if necessary.
Results:
- OK - The sensor components are OK.
Repair: Perform the following procedure in order to install the sensor assembly:
- Lubricate the O-ring with engine oil.
- Fully seat the sensor assembly in the engine.
Note: If the sensor assembly will not fully seat into the engine, replace the sensor assembly.
- Tighten the bracket bolt.
- Connect the sensor electrical connectors. Verify that the connectors are latched on both sides.
- Ensure that the harness is properly secured, and that the tie-wraps are placed in the correct location.
Proceed to Test Step 3.
- Not OK - A problem has been identified with the speed/timing sensor.
Repair: Obtain a new sensor assembly. Perform the following procedure to install the sensor assembly:
- Lubricate each O-ring with engine oil.
- Fully seat the sensor assembly in the engine.
Note: If the sensor assembly will not fully seat into the engine, replace the sensor assembly.
- Tighten the bracket bolt.
- Connect the sensor electrical connectors. Verify that the connector is latched.
- Ensure that the harness is properly secured, and that the tie-wraps are placed in the correct location.
STOP
Test Step 3. Inspect the Electrical Connectors and the Wiring
- Thoroughly inspect connectors (4), (5), and (6). Refer to Troubleshooting, 'Electrical Connectors - Inspect'.
Illustration 6 g02129242 P2 terminals that are associated with the engine speed/timing sensors
(P2-25) Primary engine speed/timing −
(P2-35) Primary engine speed/timing +
(P2-46) Secondary engine speed/timing +
(P2-47) Secondary engine speed/timing − - Perform a 45 N(10 lb) pull test on each of the wires that are associated with the engine speed/timing sensors.
- Check the allen head screw on each ECM connector for the proper torque. Refer to Troubleshooting, 'Electrical Connectors - Inspect' for the correct torque values.
- Check the harness and the wiring for abrasion and for pinch points from each sensor back to the ECM.
Illustration 4 | g01167708 |
Location of the engine speed/timing sensors (typical front engine view) (4) Harness connectors for the secondary engine speed/timing sensor (5) Harness connectors for the primary engine speed/timing sensor |
Illustration 5 | g02133273 |
(6) J2/P2 ECM connector |
Expected Result:
All of the connectors, pins, and sockets are coupled and/or inserted. The harness and wiring are free of corrosion, of abrasion, and of pinch points.
Caterpillar C32 Cost
Results:
- OK - The harness and connectors appear to be OK. Proceed to Test Step 4.
- Not OK - The connectors and/or wiring are not OK.
Repair: Repair the wiring and/or the connectors. Replace parts, if necessary. Ensure that all of the seals are properly in place and ensure that the connectors are coupled. Verify that the repair eliminates the problem.
Test Step 4. Measure the Sensor Resistance through the Engine Harness
- Disconnect the J2/P2 ECM connectors.
- If you are troubleshooting a problem with the primary engine speed/timing sensor, perform the following procedure:
- Use a multimeter to measure the resistance between P2-25 (primary engine speed/timing +) and P2-35 (primary engine speed/timing -).
- Check for an intermittent open circuit or for a short circuit by moving the harness while you take the resistance measurement. Pull the wires that are directly behind the sensor or shake the wires that are directly behind the sensor.
Resistance at 25°C(77 °F) .. 75 to 230 Ohms
- If you are troubleshooting a problem with the secondary engine speed/timing sensor, perform the following procedure:
- Measure the resistance of the sensor between P2-47 (secondary engine speed/timing +) and P2-46 (secondary engine speed/timing -).
- Check for an intermittent open circuit or for a short circuit by moving the harness while you take the resistance measurement. Pull the wires that are directly behind the sensor or shake the wires that are directly behind the sensor.
Resistance at 25°C(77 °F) .. 600 to 1800 Ohms
Expected Result:
The resistance measurement is within the specifications.
Results:
- OK - The resistance measurement is within the specifications.
Repair: The harness and sensors appear to be within specifications. There may be a problem with the ECM. Before you consider replacing the ECM, consult the Dealer Solution Network (DSN).
STOP
- Not OK - The readings are not within the specifications. The sensor resistance is not within the acceptable range when the sensor resistance is measured through the engine harness. Proceed to Test Step 5.
Test Step 5. Measure the Resistance of the Sensor
- Disconnect the harness connector for the suspect sensor.
- Thoroughly inspect the sensor connectors. Refer to Troubleshooting, 'Electrical Connectors - Inspect'.
- Measure the sensor resistance between terminals 1 and 2.
Resistance for primary engine speed/timing sensor at 25 °C(77 °F) .. 75 to 230 Ohms
Resistance for secondary engine speed/timing sensor at 25 °C(77 °F) .. 600 to 1800 Ohms
John Deere 4555, 4755, 4955 and 4560, 4760, 4960 Tractor Repair Technical Manual Download COMPLETE Technical & Repair Manual for John Deere 4555, 4755, 4955 and 4560, 4760, 4960 Tractor. It covers every single detail on your John Deere 4555, 4755, 4955 and 4560, 4760, 4960 Tractor. This manual is very useful in the treatment and repair. Download Technical Manual For John Deere 4555, 4755, 4955, 4560, 4760, 4960 Tractors Repair. TM1460 (15MAY01) This Technical Manual offers all the service and repair information for John Deere 4555, 4755, 4955, 4560, 4760, 4960 Tractors Repair. This manual contains all service, repair, maintenance & troubleshooting procedures you need to keep your machine operating smoothly, contains step-by-step instructions, diagrams, illustrations, specifications and more, everything you need to save you money and do your own repairs. John deere 4755 repair manual.
Expected Result:
The resistance measurement is within specifications.
Results: Tyranny - tales from the tiers for mac.
Caterpillar C32 Engine Pdf
- OK - The reading is within the specification. There is a problem with the wiring between the engine speed/timing sensor and the ECM. There may be a problem with a connector.
Repair: Repair the wiring and/or the connector. Replace parts, if necessary. Verify that the problem is resolved.
STOP
- Not OK - The reading is not within the specification. There is an electrical problem with the engine speed/timing sensor.
Repair: Perform the following procedure in order to check and install the new sensor assembly:
- Before you install the new sensor assembly, measure the resistance of the new sensors.
If the resistance measurements of the new sensors are within the specifications, install the new sensor assembly in the engine according to the following procedure:
- Loosen the bolt and remove the bolt that holds the sensor to the engine.
- Ensure that an O-ring is installed on the new sensor assembly. Verify that the O-ring is free of damage.
- Prior to installation, lubricate the O-ring with clean engine oil.
- Seat the sensor and tighten the bolt.
If the sensor will not seat, replace the sensor.
- Ensure that the harness is secured in the proper location.
- Verify that the repair eliminates the problem.
STOP
- Before you install the new sensor assembly, measure the resistance of the new sensors.